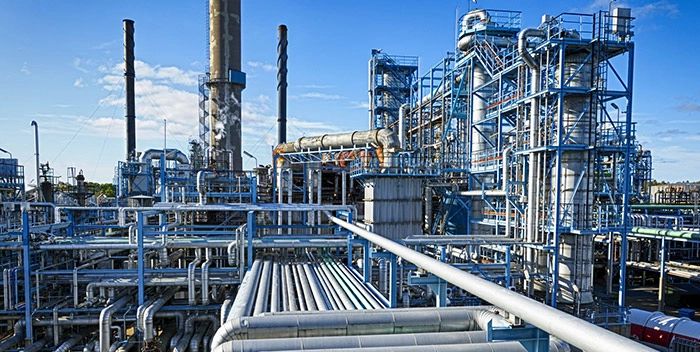
The ICB® ion-exchange filter is manufactured with one goal in mind, to remove the dissolved molecules that accumulate and cause mechanical problems in hydraulic systems and lube oil applications. These filters are engineered workhorses based on patented ion exchange technology, combining best-in-class chemistry and materials with precision robotic welding to provide the most robust filter available.
ICB is chemically engineered to remove a wide range of contamination, including acid, varnish, and metals. In EHC systems, ICB filters remove the contamination responsible for servo valve sticking, restoring fluid resistivity. ICB filters offer a step-change in performance, protecting system reliability and production with so many benefits beyond acid removal.
ICB Filters offer unmatched performance in the removal of acids, dissolved oxidation material and other molecules responsible for:
ICB filters remove the underlying cause of varnish and remove existing deposits by restoring fluid solubility, shifting chemical equilibrium back towards the original fluid condition:
While initially developed for phosphate ester lubricants back in 1992, EPT Clean Oil has expanded the capabilities of ICB filters to accommodate a wide range of lubricants and additive types.
Meet ICB RO
for Rust & Oxidation Turbine Oil
ICB RO removes varnish precursors and dissolved breakdown products continuously, breaking the accumulation cycle and eliminating the root cause of varnish formation.
Meet ICB FRF
for Phosphate Ester Fluid
ICB FRF is designed to address phosphate ester chemistry, removing acids, phenols and varnish while simultaneously improving resistivity, preventing EHC failures.
Meet ICB JET
for Aeroderivative Turbine Oil
ICB JET removes acids, oil coking precursors, and dissolved by-products continuously, breaking the accumulation cycle and eliminating the root cause of deposit formation.
Meet ICB AW
for Anti-Wear Hydraulic Oil
ICB AW selectively removes varnish and varnish feedstocks continuously, breaking the accumulation cycle and preventing varnish problems altogether.
SVR® Oil Varnish Removal System
Our engineered dialysis-style oil varnish removal system, SVR®, offers best-in-class mechanical engineering to ISO 9001 standards, chemistry management and solid contamination removal solutions. Tested and proven worldwide on 1,726 critical assets, SVR provides a step-change in lubricant lifecycle management with low maintenance demands outside of routine filter replacement.
The SVR oil varnish removal system restores fluid chemistry full-time, offering the unique advantage of removing harmful contaminants during regular turbine operation when dissolved in the oil. As a result, saturation cannot occur under any lubricant condition, preventing varnish formation.
Utilizing patented ion-exchange technology, ICB®, the SVR oil varnish removal system eliminates chemical breakdown products and varnish at the molecular level, restoring normal demulsibility values and MPC varnish potential values, and reducing Acid Number, maintaining optimal lubricant quality. Through full-time, continuous treatment, SVR stops the contamination cycle in its tracks, cleaning the lubricant every time it cycles through the dialysis circuit. Lubricant life is extended by removing and preventing chemical breakdown material accumulation, mitigating mechanical failures and costly production losses.
As the gold standard in turbine lube oil and phosphate ester fluid maintenance, the SVR oil varnish removal system is designed to facilitate rapid deployment without downtime. Just install and reap the following rewards:
Supported by a team of world experts and locally trained partners, we work hard to ensure your SVR oil varnish removal system installation is a success. Join the installation movement and protect your critical assets with an industry-leading defense shield.
It all began in 1992, when Peter Dufresne Sr discovered the step change benefit of using exchange purification technology on turbine lubricants – a result of his intimate familiarity and experience with lubricants and lubricant related failure. Successfully adopted fleet wide on 100 gas turbine compressor packages, Peter’s exchange purification began to garner further attention. When the request came from the US Department of Defense to demonstrate exchange purification on the US Navy’s carrier fleet in 1994, the possibilities for his innovation were placed on the map. This marked the beginnings of EPT Clean Oil and the launch of the ICB® filter.
Focused on providing expert advice, personable customer service and cost saving solutions that resolve lubrication issues, EPT Clean Oil mobilized on the world stage. The result – tens of millions of hours of proven performance on super-critical applications including airports, aircraft carriers, gas turbines and EHC systems at the largest power generation facilities in the world.
Today, we continue to evolve, offering advanced filtration products that remove the contamination left behind in lubricants and control fluids, focused on the root cause of mechanical failure and lubricant-related failure. Our products and services have become a game changer for our customers, offering significant cost savings and return on investment.
Sign up to hear from us.
1/6
Please reach out at your convenience so we can discuss your project.
4528 Park Serena, Calabasas CA 91302
Monday - Friday: 8am - 5pm
Saturday - Sunday: Closed